Liquid Silicone Rubber (LSR) is a two-part elastomer. It’s composed of six key elements: Base Polymers (mainly vinyl-terminated PDMS). A Cross-linker (hydrogen silicone oil). A Platinum Catalyst for rapid curing. An Inhibitor to control reaction time. Reinforcing Fillers (like fumed or precipitated silica). And various Additives for specific functionalities and processing improvements.
Composition of Liquid Silicone Rubber
A complete two-part LSR formulation typically includes:
- Base Polymers: Usually vinyl-terminated polydimethylsiloxane (PDMS).
- Reinforcing Fillers: Such as fumed silica, to enhance mechanical strength.
- Platinum Catalyst: To facilitate the addition curing reaction.
- Cross-linkers: Typically hydrogen-siloxane functional polymers, which react with the vinyl groups on the base polymer.
- Inhibitor: To control the reaction rate and extend pot life.
- Additives: Such as pigments, mold release agents, or heat stabilizers, to impart specific properties.
Let’s look into every composition next.
Base Polymers(Silicone Oil):
Polydimethylsiloxane – PDMS:Dimethyl silicone oil is the most basic and widely used silicone oil. Primary backbone polymer for most silicone rubbers (including both condensation-cure and addition-cure types). In condensation-cure silicones (like industrial-grade mold-making silicones), it acts as the main chain material.
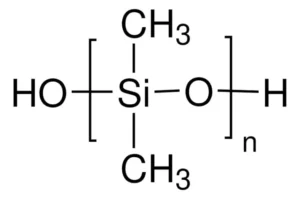
Vinyl Silicone Oil: Vinyl Silicone Oil is the primary base material for addition-cure silicones (also known as platinum-cured silicones).
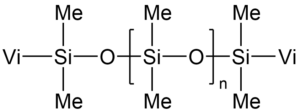
- If the vinyl content is too low, the crosslinking density of the silicone rubber will be small, resulting in low hardness and low tear strength.
- If the vinyl content is too high, the cured rubber will become harder and more brittle, and its aging resistance will decrease. Vinyl silicone oil with a small molar mass can reduce the viscosity of the rubber compound, improve its flowability, and to some extent, increase the crosslinking density of the silicone rubber, giving it certain tensile strength and hardness.
Hydrogen Silicone Oil: Hydrogen silicone oil is the key cross-linker in addition-cure silicones and in condensation-cure silicones.
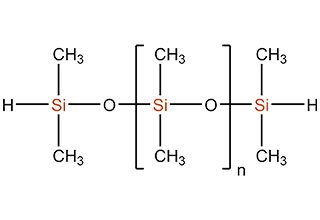
Phenyl Silicone Oil: Phenyl silicone oil is a “high-end member” of the silicone oil family. By introducing phenyl groups, it surpasses ordinary dimethyl silicone oil in temperature resistance, radiation resistance, and optical properties, primarily serving specific application fields with extremely stringent material performance requirements. Its key characteristics include excellent high/low temperature resistance (-70°C ~ 250°C+), outstanding radiation resistance, a higher refractive index (approx. 1.46 ~ 1.50), and a relatively higher cost.
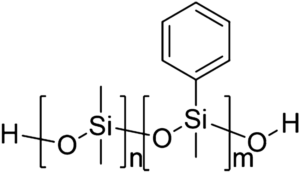
Reinforcing Fillers
Fumed Silica: Fumed silica is the core reinforcing filler in LSR, produced by high-temperature hydrolysis of silicon tetrachloride. It features nano-sized particles and a vast specific surface area. To ensure excellent dispersion, maintain low viscosity, and provide superior tensile and tear strength in LSR, its surface requires hydrophobization, also helping to maintain high product transparency.
Precipitated silica: Precipitated silica is produced via sodium silicate solution precipitation; its particles are larger than fumed silica, offering slightly lower reinforcement and transparency. While also requiring surface treatment, its primary benefit is lower cost, making it suitable for LSR applications with less stringent performance and high price sensitivity.
Platinum Catalyst
The process catalyzed by the platinum catalyst in Liquid Silicone Rubber (LSR) is, in essence, the vulcanization process of LSR. Platinum catalyst is the core of LSR’s addition cure system, efficiently catalyzing the reaction between vinyl groups and Si-H bonds for rapid liquid-to-solid conversion. It’s temperature-sensitive, controlled by inhibitors at low temperatures, but rapidly activated by heat, ensuring fast, clean curing (no by-products, maintains transparency).
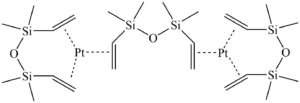
Inhibitor
The presence of an inhibitor is crucial for LSR to achieve highly efficient, automated injection molding. It resolves the contradiction of “how to prevent liquid rubber from curing immediately after mixing, yet allow it to cure rapidly in the mold. It works synergistically with the platinum catalyst to control the curing behavior of LSR.
Additives
The functions of additives are diverse and primarily include:
- Imparting Special Functionalities: Enabling LSR to possess non-inherent properties such as electrical conductivity, thermal conductivity, flame retardancy, antimicrobial properties, self-adhesion, and foaming.
- Improving Processing Performance: Optimizing LSR’s flowability and mold release, and reducing processing defects.
- Adjusting Aesthetic Characteristics: Controlling color, transparency, or surface gloss.
- Enhancing Durability: Increasing LSR’s stability during long-term use or in specific environments, such as resistance to aging and UV radiation.
Conclusion
In essence, Liquid Silicone Rubber (LSR) is a versatile material whose superior performance is precisely engineered by the synergistic interaction of its core components: base polymers (like vinyl-terminated silicone oils) forming the fundamental structure, cross-linkers (hydrogen silicone oil) building the robust network, a platinum catalyst enabling rapid, controlled vulcanization, and an inhibitor ensuring processability. Further enhanced by reinforcing fillers (primarily fumed silica) for mechanical strength and a diverse range of additives for tailored functionalities and aesthetic properties, LSR stands as a highly adaptable solution for a multitude of demanding applications.